Designing a Jet Engine Using CREO
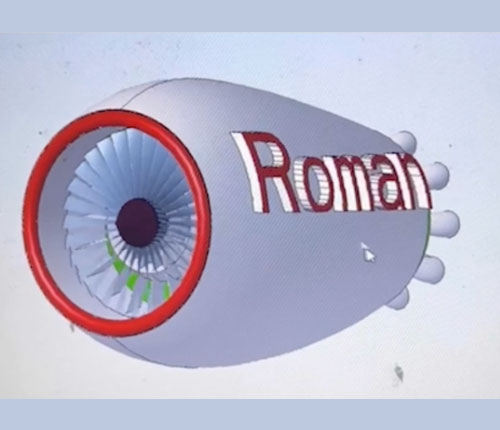
To engineer a state-of-the-art jet engine using AutoCAD, incorporating advanced aerodynamics, thermal management, and structural integrity for optimal performance and efficiency.
Background: As an aerospace-focused mechanical engineer, the objective was to design a cutting-edge jet engine that combines power, efficiency, and reliability. AutoCAD was chosen as the primary design tool for its robust 3D modeling capabilities and precise engineering features.
Methodology:
- Aerodynamic Analysis:
- Conducted extensive research on aerodynamics to optimize the engine’s air intake, compression, combustion, and exhaust processes.
- Utilized AutoCAD to model and analyze the complex geometry of airfoils, compressor blades, and nozzle designs.
- Parametric Modeling:
- Employed parametric modeling in AutoCAD to create a flexible and adaptable design that could be easily modified and optimized during the iterative process.
- Ensured accurate representation of components such as the combustion chamber, turbine, and compressor.
- Thermal Management:
- Integrated thermal management features to dissipate heat efficiently and maintain temperature balance within critical engine components.
- Conducted thermal simulations in AutoCAD to optimize the cooling system and prevent overheating.
- Structural Integrity:
- Utilized AutoCAD’s structural analysis tools to assess the integrity of components under various operating conditions.
- Ensured the materials and geometries selected could withstand the extreme forces and temperatures associated with jet engine operation.
- Assembly and Integration:
- Employed AutoCAD’s assembly capabilities to integrate individual components seamlessly into a cohesive jet engine design.
- Ensured precise alignment and compatibility between interconnected parts.
Results:
- High-Performance Design:
- Achieved a jet engine design that maximizes thrust output, fuel efficiency, and overall performance.
- Integrated advanced features to optimize the engine’s performance across a range of operating conditions.
- Efficient Aerodynamics:
- Developed streamlined components with optimized airfoil shapes, resulting in improved aerodynamic efficiency and reduced drag.
- Thermal Stability:
- Successfully managed thermal loads through strategic component placement and advanced cooling systems, ensuring stable operation under extreme conditions.
- Structural Reliability:
- AutoCAD’s structural analysis facilitated the creation of a robust engine design capable of withstanding the harsh conditions associated with high-speed flight.
Conclusion: The jet engine designed using AutoCAD exemplifies the successful integration of advanced engineering principles and digital design tools. AutoCAD’s capabilities played a pivotal role in creating a sophisticated, high-performance jet engine with optimized aerodynamics, thermal management, and structural integrity. This case study demonstrates the application of AutoCAD in pushing the boundaries of aerospace engineering, contributing to the advancement of jet propulsion technology.